What to Expect Throughout a Thorough Tank Welding Inspection
What to Expect Throughout a Thorough Tank Welding Inspection
Blog Article
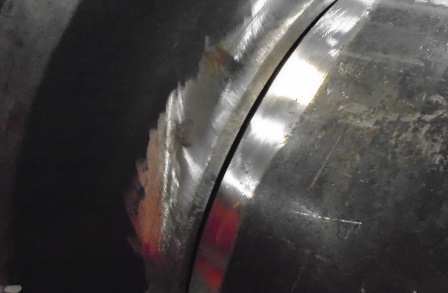
Understanding the Significance of Rigorous Tank Welding Assessment Processes in Stopping Failings and Enhancing Lifespan
In the realm of commercial procedures, the significance of rigorous tank welding inspection procedures can not be overstated. By implementing different inspection techniques, companies can detect flaws early, therefore avoiding pricey repercussions and extending the life of their storage space tanks.
Relevance of Welding Inspections
Acknowledging the important function of welding assessments in preserving structural stability, these procedures guarantee that welds fulfill recognized criteria and specifications - Tank Welding Inspection. Efficient welding inspections are vital in the building and maintenance of storage tanks, as they directly affect the resilience and safety of the frameworks. By determining potential deficiencies, such as inappropriate methods or material issues, assessments reduce the risk of tragic failings
Welding inspections incorporate different approaches, consisting of aesthetic examinations, non-destructive screening (NDT), and evaluations of welding treatments. Each technique serves to verify the top quality and compliance of welds with sector policies, thereby securing both personnel and ecological passions. In addition, routine examinations foster a culture of accountability and quality within the labor force, making sure that all group members adhere to finest techniques.
In addition, these evaluations add to the total lifecycle monitoring of containers by identifying wear or degradation early while doing so. By addressing these problems proactively, companies can prolong the functional life expectancy of their properties, ultimately bring about cost savings and boosted reliability. In summary, the value of welding inspections can not be overemphasized; they are vital for making sure safety, longevity, and compliance in tank building and upkeep.
Typical Root Causes Of Tank Failures
Comprehending the typical root causes of tank failings is vital for avoiding disastrous occurrences and guaranteeing the long life of storage systems. One widespread reason for storage tank failure is deterioration, which can considerably deteriorate the architectural honesty of containers with time. Ecological elements, such as direct exposure to wetness, chemicals, and temperature level fluctuations, can increase this process.
One more critical factor is incorrect welding techniques, which might lead to flaws like splits or insufficient joints. These issues can jeopardize the tank's stamina and bring about leakages or tears. Furthermore, poor upkeep methods can cause undetected deterioration, ultimately raising the risk of failing.
Style imperfections, including insufficient thickness or bad product choice, can likewise add to tank vulnerabilities. In addition, functional elements, such as overfilling or direct exposure to severe pressures, can strain the tank beyond its designated restrictions.
Secret Examination Techniques
Efficient inspection strategies play a crucial duty in alleviating the risks related to container failures. A thorough technique to tank welding assessment includes numerous crucial methods, find out here now each created to determine prospective flaws and ensure architectural stability.
Visual assessment remains the very first line of protection, allowing assessors to recognize surface area anomalies such as splits, deterioration, or imbalance. This strategy is commonly supplemented by non-destructive screening (NDT) techniques, which are vital for examining weld top quality without endangering the storage tank's honesty.
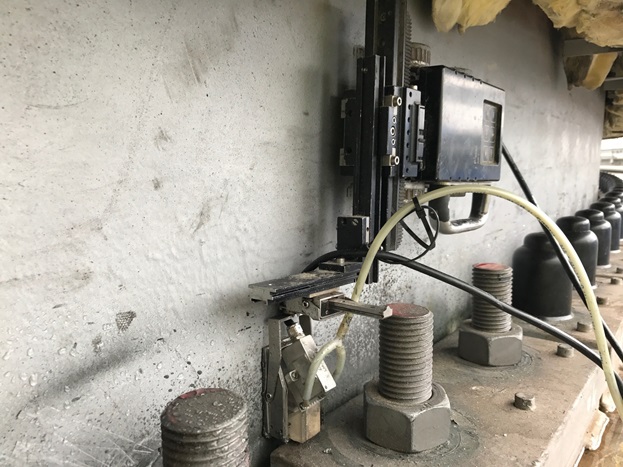
In addition, magnetic bit testing (MPT) and dye penetrant testing (DPT) are reliable for spotting surface flaws internet in ferromagnetic materials and non-porous surfaces, specifically. Each strategy has its toughness and constraints; for that reason, a combination of approaches is typically utilized to accomplish comprehensive examination outcomes.
Advantages of Strenuous Evaluations
While the immediate expenses of strenuous inspections may seem challenging, the long-term benefits substantially exceed these first financial investments. Carrying out complete inspection processes not just improves the honesty and safety and security of storage tank frameworks but also lessens the danger of tragic failures that can result in considerable financial losses and ecological harm.
Strenuous assessments assist identify possible concerns early in the welding process, permitting prompt corrective activities that prevent costly fixings or replacements down the line. This positive strategy promotes a society of quality assurance, where adherence to finest methods comes to be ingrained in operational procedures. Regular inspections add to increased possession durability, as they guarantee that containers stay in optimum condition throughout their lifespan.
Furthermore, the paperwork generated from these examinations offers as a beneficial resource for upkeep preparation and performance evaluations. This data-driven approach can likewise boost operational effectiveness, leading to reduced downtime and improved efficiency. Ultimately, strenuous evaluations not only protect the structural honesty of storage tanks but additionally offer significant financial advantages, reinforcing the concept that purchasing quality control is a wise choice for any organization included in storage tank operations.
Regulatory Criteria and Compliance
Regulatory standards and compliance are essential parts of storage tank welding evaluation procedures, as they develop the structure for guaranteeing security and high quality in operations. Compliance with these requirements not only minimizes dangers however likewise improves the total stability of welded frameworks. Different companies, including the American Culture of Mechanical Designers (ASME) and the American Petroleum Institute (API), supply standards that determine appropriate practices for welding, evaluation, and screening.
These standards mandate using certified workers, the execution of extensive examination protocols, and adherence to certain welding treatments. By aligning with regulatory demands, organizations can make sure that their containers satisfy the necessary security and performance criteria, thus minimizing the probability of tragic failures that can bring about substantial financial losses and ecological damages.

Moreover, regulatory compliance promotes a society of liability and continual improvement within the welding and construction markets (Tank Welding Inspection). Normal audits and evaluations ensure that practices continue to be lined up with developing criteria, therefore advertising long-term integrity and operational performance. Inevitably, adherence to governing criteria not just shields properties but likewise enhances the life expectancy of bonded containers, guaranteeing they offer their designated objective successfully gradually
Final Thought
In final thought, strenuous storage tank welding inspection processes play an important function in avoiding failings and expanding the life-span of storage structures. By identifying her comment is here prospective shortages via various examination strategies, companies can reduce dangers connected with storage tank integrity.
Report this page